Are Right To Repair Laws Working? A Case In California Holds Some Clues.
California's Attorney General launched an inquiry into soldering iron maker American Hakko Products' compliance with the state's right to repair law. It is already bearing fruit.
The company that is the subject of an inquiry by California’s Attorney General over its compliance with the state’s newly enacted right to repair law has started to make more repair information available to customers, according to the independent repair shop owner who filed the complaint.
Steven Rhine, the CEO of Rhine Labs in Vancouver, Washington, said that American Hakko Products (AHP), a leading manufacturer of soldering irons, released firmware he requested for two soldering stations. That came after the California Attorney General informed Hakko in November that it was conducting an inquiry of the company in response to a complaint Rhine submitted to the AG’s office in late July.
Rhine submitted the complaint after AHP did not adequately respond to a request for access to “repair documents for 3rd party servicing” of two Hakko products: the FM-203 and FM-205 soldering stations.
Independent repairer looks to flex new repair rights
Rhine owns Rhine Labs, a Washington-based shop that repairs control boards for Computer Numerical Control (CNC) machines like mills, lathes, elevators and other equipment owned by small businesses. He counts a number of California firms among his customers and HAKKO soldering stations are an important part of his business operation.
In an interview with Fight to Repair News, Rhine said that an FM 203 device that he used suddenly “went dead.” Repairing it required him to replace a failed micro controller on the device, and that required access to the Hakko firmware as well as device schematics and a detailed service manual, but that AHP refused to provide that information.
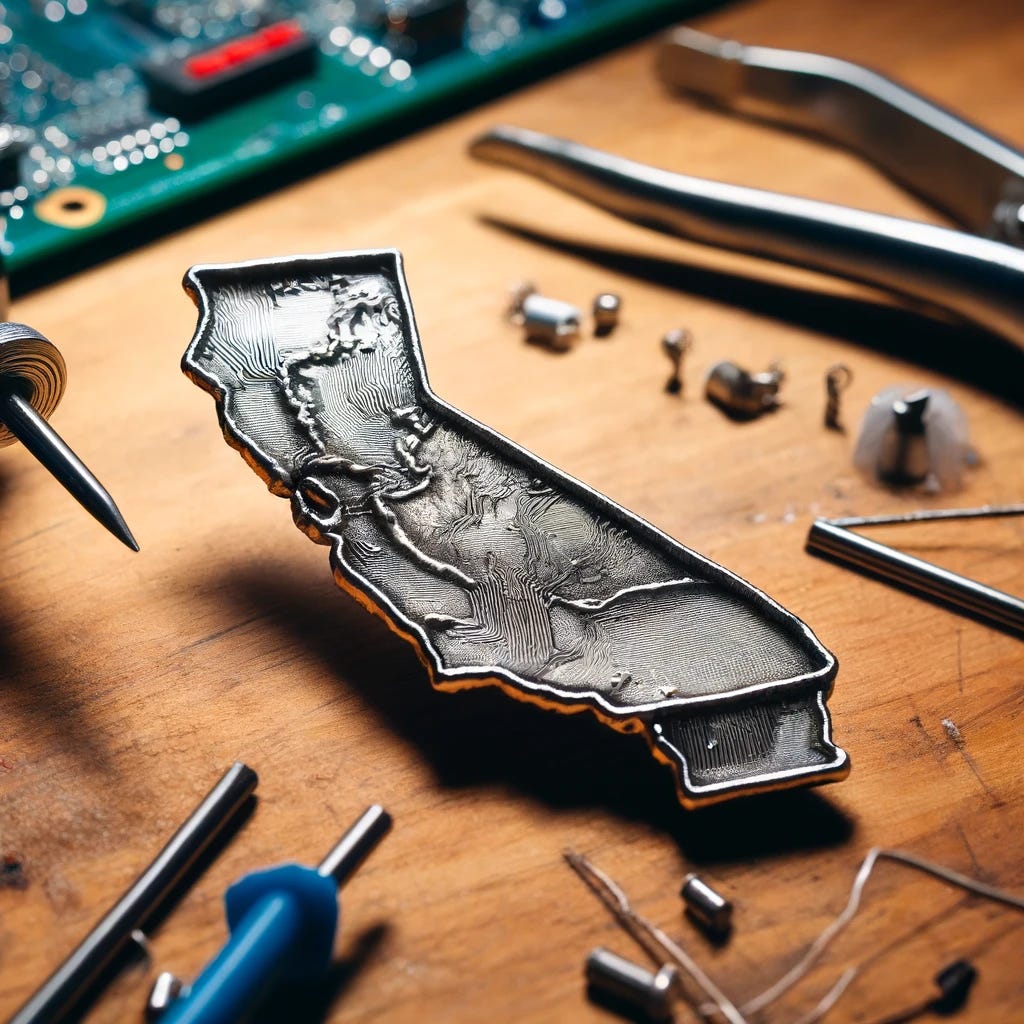
California’s right to repair law, known as Senate Bill No. 244 (or SB 244) requires manufacturers that produced a product sold to consumers in California for $100 or more within the last least seven years to provide them and independent shops with repair information, parts and access to software and other tools for covered products. AHP failed to make such information available for many of its products, Rhine alleged. In other cases, the “repair manuals” it posted were simply re-worked user manuals with supplemental information on assembling or disassembling their electronics, Rhine said.
» Premium subscribers get early access to our original reporting, as well as early access to our newsletter content, podcasts and opportunities to participate in live, virtual events. Use the button (below) to subscribe now! «
In response to Rhine’s request, Chris Stuber, the Vice President of the Product Division at American Hakko Products, said in an email to Rhine that the company was in the process of updating its service manuals to meet with the requirements of the new law and already provided firmware for newer HAKKO products.
“We …believe in providing information and assistance needed to allow customers to make their own repairs,” Stuber wrote on July 1st, according to a copy of the email shared with Fight to Repair News.
Hakko: Schematics “not needed for repair”?
However, Stuber’s email to Rhine also cast doubt on whether AHP intended to fully comply with the language of California’s law. For example, schematic diagrams - generally considered part of the documentation needed to carry out repairs on electronic devices - would not be provided, Stuber declared.
“Detailed schematics used to build the PCBs are controlled by Hakko Corporation and are not required to effectively repair the product,” he wrote.
Stuber also floated the idea to Rhine that his company was exempted from compliance with the law as soldering tools the company sells were “industrial” rather than “consumer” goods and therefore not covered by SB 244, California’s right to repair law, which includes an exemption for industrial equipment.
Soldering stations = industrial tools?!
Those suspicions were confirmed after Stuber (accidentally?) copied Rhine on an internal email that suggested the company was looking for ways to sidestep SB 244. compliance. In the email, Stuber repeats the assertion that “schematic diagrams are not required to effect repairs” and notes that its parent company, HJ (Hakko Japan), “had interpreted the business and professional code of California as a possible exclusion for our products, which are industrial tools,” according to a copy of the letter shared with Fight to Repair News.
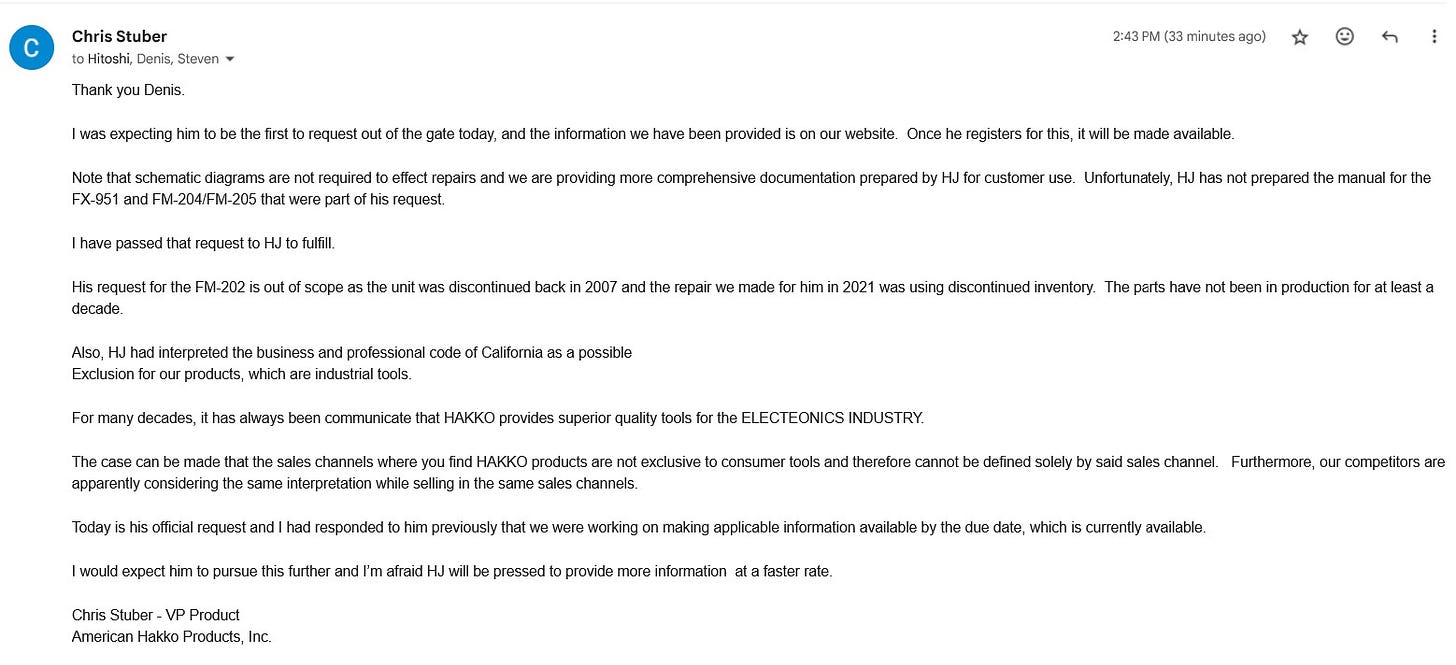
“The case can be made that the sales channels where you find HAKKO products are not exclusive to consumer tools and therefore cannot be defined solely by said sales channel.” Hakko’s competitors “are apparently considering the same interpretation while selling in the same sales channels,” Stuber wrote.
AG’s Office launches inquiry into Hakko
After weeks of back and forth with Hakko, Rhine submitted a complaint to the California Attorney General, Rob Bonta, on July 29th arguing that Hakko, which is based in Valencia, California, was not complying with SB 244.
More than three months later, on November 17th, Rhine received a letter from Attorney General Bonta saying that it had forwarded a copy of his complaint as well as an “inquiry from our office” to AHP. “Hopefully this will elicit a response from them that we all find satisfactory,” the letter read.
Soon after, Rhine said, AHP uploaded copies of the firmware for the soldering stations he had inquired about to the company’s online knowledge base, kb.hakkousa.com on December 3rd. Rhine wrote that Stuber informed him that AHP was in the process of revising the FM-203 repair manual, as well.
AHP and Stuber did not respond to multiple requests for comment. We will update this story if and when they do.
Encouraging signs on compliance
Rhine’s experience with AHP suggests that state right to repair laws may start to have an impact on corporate behavior as attorneys general step up to enforce the new laws.
Rhine noted that a similar engagement with the firm Tormach, a manufacturer of CNC machines, in 2021 resulted in the company publishing a comprehensive collection of repair materials for its equipment, including schematics, firmware, documentation and parameter files to GitHub, the cloud based open source code repository that is a common platform for sharing information online.
“If we can get R2R enforced, it will make it more viable to do business,” said Rhine. Tormach’s embrace of right to repair and willingness to share the information needed to complete repairs made it “economically viable to repair boards” for small businesses that rely on the company’s technology, he said. “If I had to sit there and draw my own schematic that’s three hours at $135 an hour for my client to reverse engineer it,” he said. “People can’t afford to pay that.”
Those higher costs push small businesses to replace rather than repair, or subject themselves to exorbitant costs for repair from authorized repair providers, Rhine said.
Schematics and the battle(s) to come
But Rhine notes that AHP’s retreat on supplying firmware for a couple of soldering stations doesn’t make it compliant with the California law. “The war is not over yet,” he said. “My quest is for schematics and firmware for everything (AHP) manufactured from July 1st 2015 to today,” he said, invoking the state of Oregon’s requirement in its right to repair law that manufacturers make available repair information for any products manufactured since 2015.
With many AHP products still lacking service manuals, schematics and other information needed for repairs, there is more work to do, he said. And the company’s flirtation with non-compliance, citing exemptions written into the California law or contesting whether schematics are needed for repair are concerning, he said.
As the AHP inquiry moves forward, Rhine is also reaching out to other equipment vendors that his repair business relies on within similar requests for repair information and tools.
“My hope is to get more compliance and hold more companies’ feet over fire,” Rhine said. “I hope we see it go from a flat ‘no,’ to ‘we’re working on it’ and ‘we’re making progress,” he said.
Nathan Proctor, the Senior Director of the Right to Repair campaign at US PIRG, the Public Interest Research Group, said the interest of people like Rhine in obtaining the information needed to complete repairs wasn’t a surprise.
"Manufacturers have spent decades cutting back on the repair information they share, even with their most experienced and proficient customers. People want to be able to fix stuff, and there are a lot of really skilled technicians out there who could repair a lot more if they had access to the right materials,” he said. “Hopefully this is a trend that continues."
Editor’s note: an earlier version of this story contained a misspelling of the last name of American Hakko Products’ Vice President Chris Stuber. The story has been corrected. - Dec 13, 2024
Editor’s note: an earlier version of this story misquoted Steven Rhine. He is seeking repair documentation for products produced before 2015 not 2017 as stated, based on language in Oregon’s state right to repair law rather. Also: Mr. Rhine’s hourly shop rate is $135 an hour. The story has been corrected. - Dec 13, 2024